Tapping into the future of warehouse robotics — Part 1
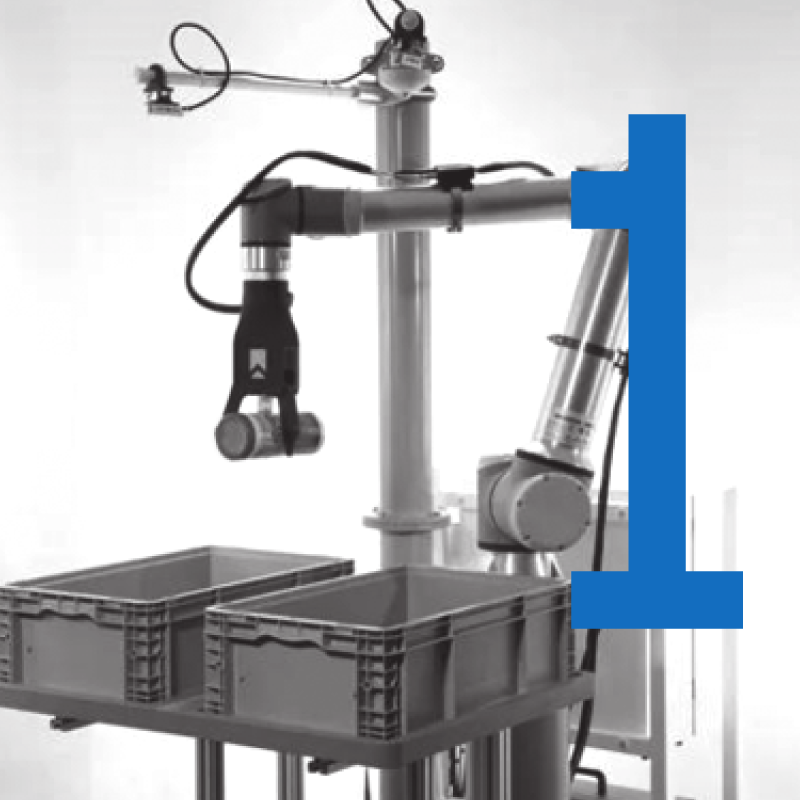
Tapping into the future of warehouse robotics — Part 1
Changing consumer preferences have created radically different needs for modern warehouse operators.
Warehouse and distribution facilities exist at the center of e-Commerce supply chains, with automation a foundational enabler for driving efficiency. Warehouse automation handles many repetitive tasks related to movement of goods that might otherwise be performed by a human. Traditional forms of automation such as conveyors, sorters, and various forms of robotics are highly effective in applications that require handling of bulk goods or fixed stock-keeping units (SKUs) where the process to be automated is highly structured and predictable.
However, changing consumer preferences have created radically different needs for modern warehouse operators. They must dynamically fulfill and assemble individual orders consisting of rapidly changing and diverse SKUs as use cases move away from bulk deliveries. Today, the primary source of competitive advantage is operational efficiency, minimizing fulfillment costs and maximizing delivery speed.
Amazon is driving much of the innovation in the e-Commerce sector, constantly pushing greater order flexibility, faster delivery times and lower costs for consumers. They were one of the first to adopt more advanced warehouse automation as an enabler for improved order handling capabilities when they acquired Kiva Systems for $775M in 2012. Last year, they had over 200,000 robots in their warehouses working alongside humans. Most recently they acquired Canvas, a company specializing in “spatial AI” where mobile robots can autonomously navigate in dynamic situations.
According to McKinsey & Co., US e-commerce purchase volume rose from 16% penetration at the start of 2020 to nearly 35% at the end of Q1, driven by the COVID-19 Pandemic. That’s 10 years of growth in just three months. Retailers around the world had trouble fulfilling orders due to customer demand, logistical delays and trade tension.
To accommodate, Amazon hired 175,000 new employees in March and April and is opening new fulfillment centers leveraging human and robotic technology in new locations at an accelerated rate. For the entire warehouse industry, operators discovered that automation is a core enabler for not only operational efficiency, but also ensuring business continuity during workforce disruptions brought on by social distancing needs.
Design principles for the next generation of robotics start-ups
At F-Prime Capital, we are fortunate to have learned from many warehouse robotic companies and seen first-hand how automating certain activities enables humans to focus on higher-value activities. A new generation of robotics start-ups are disrupting the warehouse automation market by offering a fundamentally different value-proposition to warehouse operators. These guiding principles enable start-ups to quickly overcome barriers to adoption and build capital efficient businesses than was historically possible in this sector, and they are a major reason for the increasing investor excitement in the space.
1) Scalability: Traditional automation solutions are deployed as monolithic solutions — they basically transform the entire process that they are replacing. While they can be effective, it is a high capex decision that often requires a multi-million-dollar upfront investment. In addition, if there are any changes in the process — e.g., product changes, workflow changes, or volume of demand changes — such solutions typically cannot adapt without significant further investment.
Many of the newer generation of warehouse robotics are designed to operate within the existing flow of work. In other words, they can operate alongside a human to increase productivity, or they operate within existing workcells. For example, pick-assist robots work alongside a human to reduce walking time. In doing so, the solutions can be deployed incrementally (e.g., supporting only a portion of the staff or replacing only a subset of workcells) and can be scaled up or down as needs dictate. This not only eliminates the need for massive upfront investments, it also enables more adaptability as processes change.
2) Resilience: Typical automation solutions are designed to perform repetitive tasks with high accuracy and high speed. They rely on simple sensor inputs, such as barcode scanners or binary I/O devices, to measure the world around them and perform their pre designed task. However, they expect the operating environment to be highly controlled, and in case something unexpected happens, a human operator is required to reset the system.
Advances in computer vision and machine learning have given modern robotics much greater environmental ‘awareness’. These solutions are more resilient to changes in the environment and provide an operating envelope in much less structured environments. For example, mobile robots can automatically avoid obstacles and piece-picking robots can automatically adjust their picking trajectory based on the orientation of the object to be picked.
3) Ease of Integration: Integration of warehouse automation is one of the biggest obstacles to adoption and can often lead to a multi-year cycle of refreshing or adding automation solutions. Given that traditional solutions are monolithic in nature, they require an ‘all-or-none’ deployment decision that leaves little flexibility for integration with existing forms of automation. Such solutions also lead to a desire to do more customization for each deployment, which further inhibits integration with other solutions.
With newer forms of automation focused operating within the existing flow of work, they are also focused on building standardized solutions with out of the box integrations to existing automation solutions. This can include the warehouse management system operating the warehouse or the complementary automation systems that exist up and downstream in the workflow. The ease of integration enables more rapid experimentation with new solutions, and it drives much faster time to value for the operator.
4) ROI at lower costs: For warehouse operators, automation decisions are fundamentally driven by capital budgets and return on investment. As new robotics companies enable more scalable deployments, upfront costs are inherently lower. Falling sensor costs and falling costs of industrial-grade robot arms are also helping reduce deployment costs. Many players are even starting to experiment with ‘as-a-Service’ business models which convert capital costs to operating costs and allow for shorter term deployment. Such models are enabled by standardized solutions which allow providers to reuse solutions for differentiated customers.
RightHand Robotics
F-Prime Capital is excited to announce its investment in RightHand Robotics (RHR). In addition to its world class team led by Yaro, Leif, and Lael, RHR exemplifies all the best design principles of the next generation of robotics companies. RHR has also shown what it takes to create a successful business in the warehouse logistics space — demonstrated success across a range of customer segments and use cases, multiple referenceable production deployments, and a broad set of partnerships with both adjacent technology providers and system integrators. You can see a small glimpse of what RightHand has accomplished in this video case study with Paltac, one of its anchor customer deployments.
In part 2 of the series, I will discuss the broader category of warehouse robotics start-ups and some of the emerging use cases that are starting to see success.